POA appeared on the Italian “INTERNI” design era
POA appeared on the Italian “INTERNI” design era
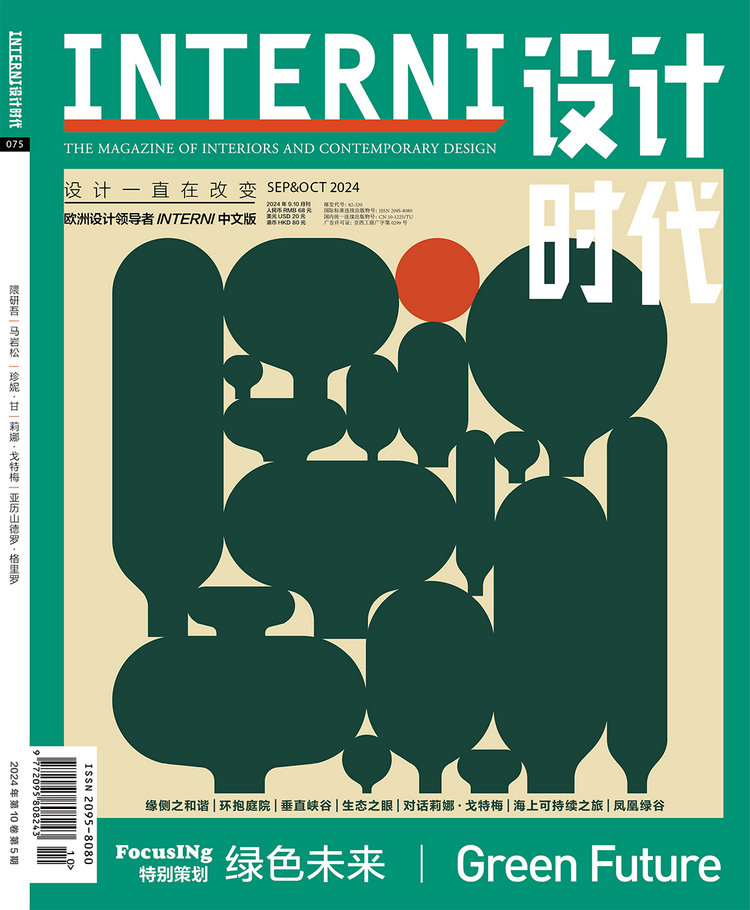
Please click on the QR code at the end of the article
or read the original text, to pre-order this issue
INTERNI International Edition Issue 5 Volume 10, 2024
Special Issue: Green Future (Green Future)
Founded in Italy in 1954, INTERNI magazine is an authoritative professional design magazine that selects the latest developments and trends in the Italian and international design world. It is the most famous European architecture, interior and product design magazine. Each issue has the latest interior architecture (home, industrial products, offices) and individual works similar to design. It has unique design sense and humanistic spirit. Design cases, architectural concepts, etc. and infect and inspire readers through vivid text and visually impactful photography. It is also the leader and operator of Milan Design Week.
For 60 years, she has narrated, illustrated, and commented on Italian design, giving Italian design a chance to speak. But INTERNI is not just a magazine about design. She is also a collector of creative power and energy and the center of various design activities, exhibitions, gatherings and academic conferences. It is currently the most popular design magazine in the world. It can be said that INTERNI is a magazine, a brand, and even more a “world of design”.
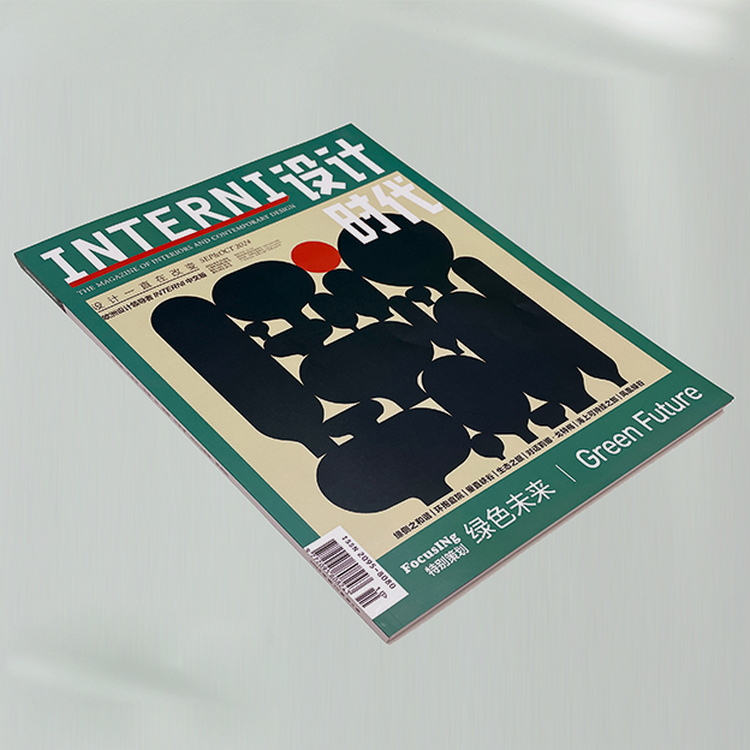
This album “INTERNI” also includes the works of six architects and their firms as special albums.
They are: Kengo Kuma—Harmony on the Edge, Antonio Zagaria—Embracing Courtyard, Ma Yansong/MAD Architects—Vertical Canyon, Gan Architecture Studio—Ecological Eye, Pan Chengshou/POA Architects—Phoenix Green Valley, Kvonen Design Studio/Norme Architects—Sustainable Journey at Sea. Special thanks to “INTERNI CHINA” for its role as a bridge in the publication of this album and its efforts to promote architects to the international architectural stage.
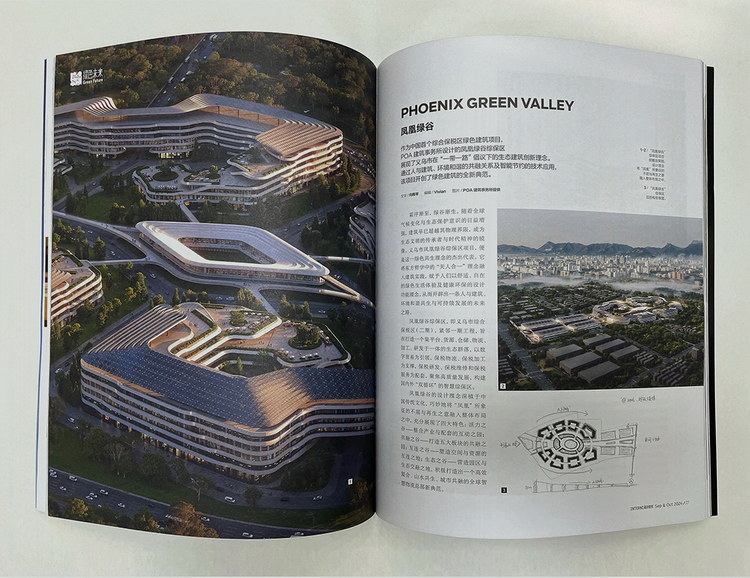
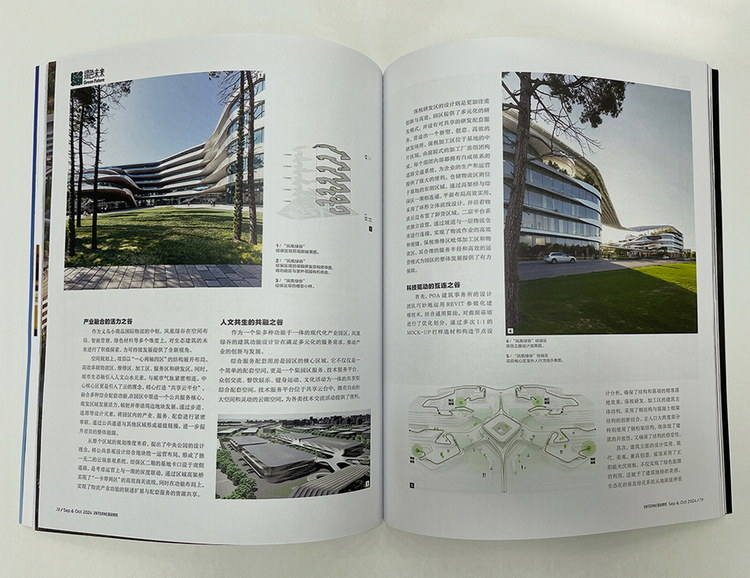
Pan of Architects (POA) is a collective of architects, designers, and engineers from across the country working together to build a better future.Official website Address:https://en.i-poa.com/